Ultrasonic Cleaning Technology
Overview
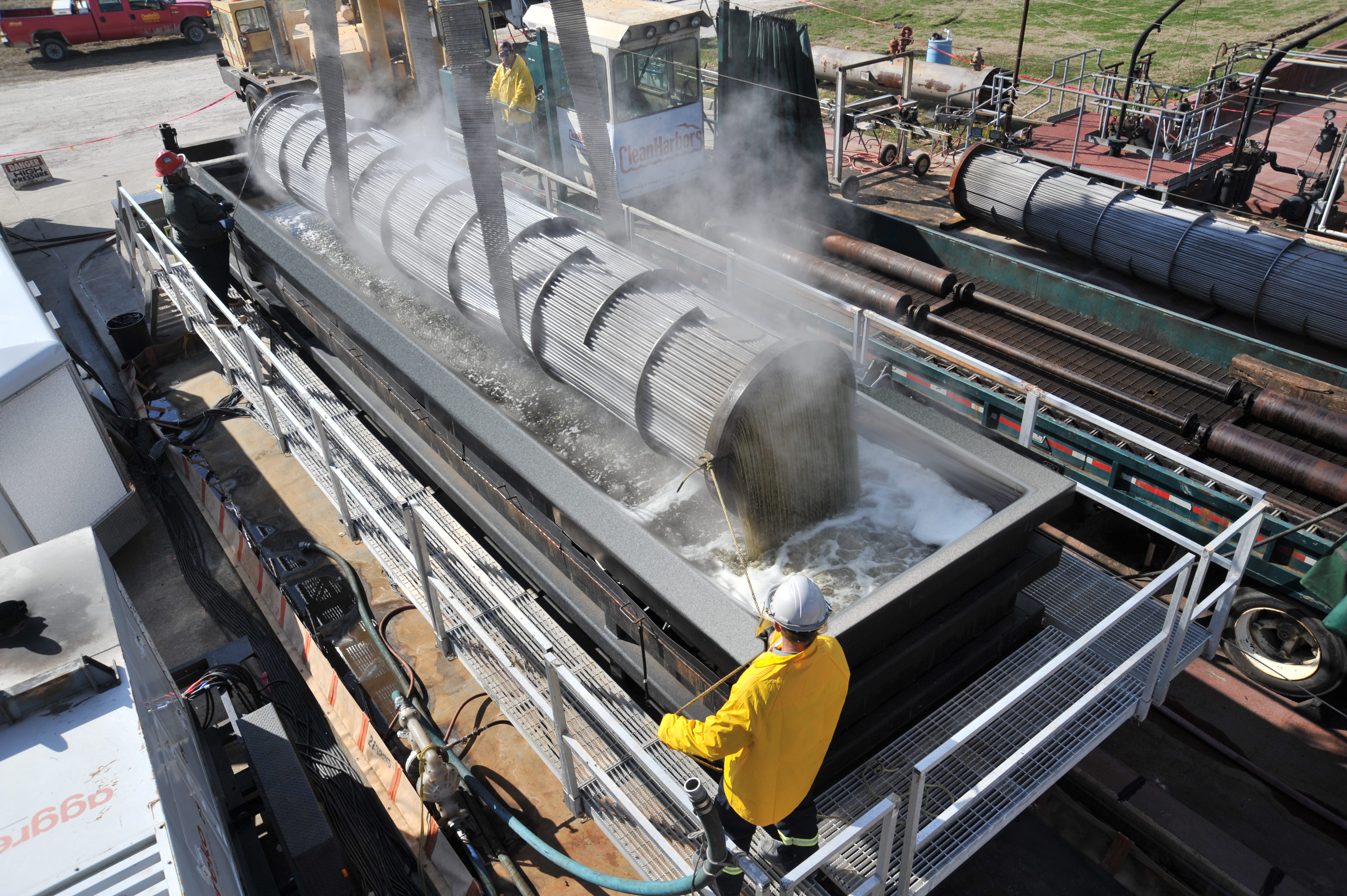
HPC Industrial is a leader in the industry for Ultrasonic Cleaning Services. Our dedication to technological advancement, sustainability and cost-effectiveness sets us apart from our competitors. We have the expertise and resources necessary to provide comprehensive solutions that will keep any facility running smoothly.
HPC’s Ultrasonic Cleaning can remove various scales and deposits from industrial equipment through immersion in a size-engineered ultrasonic bath. Often combined with low- or high-pressure water cleaning to help rinse away residual chemicals and foulant, ultrasonic cleaning is a powerful technique that helps return heat exchangers and other industrial parts to peak performance.
The ultrasonic cleaning vessel is equipped with ultrasonic transducers that deliver acoustic energy to the equipment surface, pushing away stuck-on deposits, breaking down tough scales and getting right down to the bare metal, removing even the thinnest of films. The chemistry selected for the cleaning process is specially designed to be compatible with the fouling type and the metallurgy of the material, ensuring that we deliver the utmost care to your assets.
Advantages of Ultrasonic Cleaning
- Interstitial areas are easier to reach
- Improved heat-transfer coefficient rates
- Improved volume throughput
- Lower fuel gas consumption resulting in reduction of greenhouse gas emissions
- Reduction of water consumption by 75% - 95% versus high-pressure water blasting alone
- Reduced manpower onsite, removing personnel from line of fire
- Reduction in overall turnaround time for traditionally difficult to clean assets
- Ready for NDE inspection after one round of cleaning
Targeted Chemistries
Over 25 years of research and development has gone into the creation of our line of proprietary chemistries. The Paratene® chemical product line, trademarked under Clean Harbors, offers several blends that have been tested and proven to be the best in the market for industrial ultrasonic applications.
- Degreasing – Our base chemical blend for removing hydrocarbon deposits has a proven record of removing heavy and light bitumen, asphaltenes, tars, polymers, greases, waxes and other hydrocarbon-based products. Several chemical additives can help boost the application of this blend towards certain foulant types, including pyrophoric iron polysulfides, polyolefins and coked or shellacked materials.
- Descaling – Our base chemical blend for removing inorganic scales, such as hard water scales and rust, sulphates, carbonates and other acid-soluble materials. This inhibited organic acid blend can also be boosted with specialty additives to help target tougher inorganic foulants where necessary.
- Specialty blends – The Paratene® line also offers several other ultrasonic-compatible blends that help target specific foulants such as silicates, paint and clear coats, biofilms, and carbonized sugars.
Ultrasonic Capabilities
As part of our Ultrasonic Cleaning technology, we offer multiple sizes of ultrasonic vessels geared toward the cleaning of heat exchangers, components or other parts such as valves, fittings, demister pads, flame arrestors and scaffolding. Smaller vessels and parts washers are also available through our sister company, Safety-Kleen.
Ultrasonic Solutions
Don’t settle for a “one size fits all” approach when it comes to cleaning your facility’s equipment. HPC Industrial offers multiple solutions to help you maintain your equipment and avoid costly shutdowns.
- Mobile Services – Ideal for turnarounds and larger scale projects
- Dedicated Wash Pad Services – We can assist with the conversion of your traditional wash pad to an Ultrasonic Cleaning wash pad
- Offsite Cleaning Facility – Turnkey cleaning services including Ultrasonic Cleaning, high-pressure water blasting, mechanical, inspection, transportation and waste handling
Read more about how HPC Industrial is an industry leader in the white papers, case studies and selected book sections below, written by HPC employees.
- “The Application of Industrial Scale Ultrasonic Cleaning to Heat Exchangers” B. Kieser, R. Philion, S. Smith, T. McCartney (2011)
- “Ultrasonic Cleaning of Badly Fouled Compabloc Exchangers” R. Philion, S. Smth, B. Kieser, T. McCartney (2011)
- “The Effective Removal of FeCO3 Deposits From Critical Process Heat Exchangers Used in Ammonia Production Using a Proprietary Ultrasonic Chemical Cleaning Method” R. Philion, T. McCartney (2013)
- “Ultrasonic Chemical Cleaning: The Development of Chemical Blends for Industrial Applications” R. Shank, T. McCartney, R. Philion (2021)
- “Chemical Cleaning of Crude Oil Fouling Deposits; Applying the Coke Spectrum” R. Shank, T. McCartney (2022) *Also to Appear in a Special Edition of Heat Transfer Engineering (Aug/Sept 2023)
- “Simultaneous Effective Removal of Iron Polysulfide and Polyolefin Fouling from Twisted Tube Heat Exchangers in Hydrocracker Process using Ultrasonic Chemical Cleaning” R. Shank, T. McCartney (2022)
- “Technology for Chemical Cleaning of Industrial Equipment, 2nd Edition” W.Frenier (2018) Acknowledgement for Ultrasonic Chemical Cleaning section given to T. McCartney, R. Shank
Download Fact Sheet (Ultrasonic Cleaning Services)
Customer Testimonials
“For every dollar we spend on Ultrasonic Cleaning, we save four dollars in operational and cost efficiencies. We used to have to throw out most of the components as they could not be put back into production. Our capital costs have reduced dramatically.” - Suncor Energy | Fort MacMurray, AB
“We experienced excellent results with cleaning components for off-site repair/overhaul. Third party companies have never seen valves as clean as the ones coming from Scotford. Stainless steel bundles were cleaned better than expected and typically achieved IRIS quality. Bundles with other material composition were generally cleaned to Eddy Current quality. To achieve IRIS spec for these non-stainless items, some were rinsed with a 20Kpsi & rotary lance.” - Shell | Scotford, AB
“We achieved a 27% increase in production of Ammonia after Tech Sonic cleaned our C-109 process train heat exchangers.” - CF Industries | Donaldsonville, LA
“The Refinery decided to test clean four Compabloc units using the new process proposed by Clean Harbors. With the clean Compablocs back in operation, the refinery client captured the throughput and heat transfer data rates to reveal an annual (bpd) recovery of US$4.27M.” - Shell | Sarnia, ON
“We saved over $6M in LPO from the addition 2-4 months in extended run time achieved after Ultrasonically Cleaning our Twisted Tube Heat Exchangers from the HC Reactor. We had to reduce to pressure in the unit upon startup by over 15%. When the exchangers came out of the Ultrasonic vessel, they looked like they had come straight from the manufacturer. With hydroblasting alone we would spend eight days per exchanger but with Ultrasonics each exchanger was done in a shift.” – Marathon | Carson, CA
“The previous clean on our Compabloc exchanger came back with a volume throughput of only 49%, we use Ultrasonic cleaning from Clean Harbors this time and returned out throughput to better than 80%” – Cenovus| Lima, OH